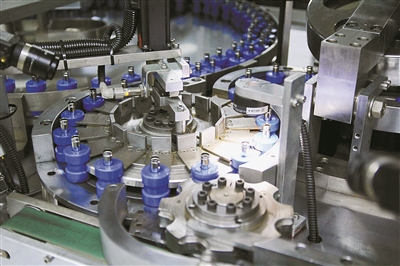 |
野马电池新一代智能电池生产线。(野马电池股份有限公司供图) |
见习记者 徐卓蔚 轰鸣的生产线上,功能各异的自动化机器高速运转,产品在这里生产、组装,然后飞向海内外。平稳有力的机械手、操作自如的搬运机器人……智能化改造后的生产线,“机器换人”、减员增效。 走进野马电池股份有限公司新一代智能电池生产车间,记者看到寥寥数人看管着生产现场,车间的主角是一整条畅通快速的生产线,零散的原料通过传送带有序转入下一道工序,经过多道自动化组装,电池产品就在这一条线上完成了。 “每条碱性电池生产线的用工人数从原来的5人减少到1人,每台包装设备的用工人数也能减少1人至2人。”野马电池两化办经理王建裕告诉记者,智能工厂项目建成后,平均生产效率可以提高20%,目前每条生产线每分钟可生产600颗碱性电池,平均每天产能从60万颗提升到70万颗,电池的订单周期从45天缩短到30天。 智能化改造后,不仅生产效率提上去了,产品质量也因此得到了提高。记者看到,生产线上安装了自动化质检机器,在生产过程中进行实时质量检验,自动剔除质量异常产品。“生产线上产品不良率降低了25%,产品报废率由原来的2.8‰下降为2‰以下。”王建裕告诉记者,在确保产品达到高档次要求的同时,还降低了原料的损耗和产品的综合能耗,单位产品能耗降低了15%,低于同行业及宁波市现有能耗强度控制目标值。 生产现场布置了大量可视化看板,可以随时查看对应的生产任务进度和相关的人员、机器、物料等信息,实现了对生产过程的精细化管理。通过大数据平台,办公室的电脑上能实时观测生产进度。 车间内,记者看到智能机器人在接收系统指令后,开始将生产线上打包成盒的电池搬运至固定的存放区域,并随手将空盒安放至生产线上。待电池装满一托架后,系统就会发送指令运送电池。 “从销售成本计算到销售订单生成,从生产任务派发到完工汇报,从设备状态到工艺参数,从质量检验到产品追溯,从采购入库到销售出库,所有环节实现了数字化、透明化。”以此为基础,创建顾客档案APP,顾客的每一款产品都可以通过APP查询到对应的电池生产信息、过程检验信息以及实验室放电数据,涵盖人、机、料、法、环的产品全生命周期信息。 “智能化升级打通了从原料车间到半成品车间到包装车间的信息屏障,实现了数据互联、生产管控、品质管控、物料配送、AGV控制等,从而借助‘人机协作’,推进精益生产,提高生产效率。”王建裕告诉记者,智能制造不仅是大势所趋,更是企业面临人工成本增加、制造成本高、部门间协同差等问题时亟须突破的主观追求。 目前,野马电池智能化进程仍在继续,“智慧野马4.0”深度融合应用新一代信息技术,广泛应用5G、数字孪生、物联网、人工智能、工业互联网等技术,开启智能工厂战略,大力推进系统集成平台的开发,建立企业级大数据平台,实现生产数字化、制造协同化、管理智慧化。
|